Introduction: Why This Matters Now
In today's tense social and political climate, workers across all industries are increasingly finding themselves involved in or near public protests. These events may be rooted in calls for justice, policy changes, or labor rights, but they can also occur quickly, with little warning, and sometimes escalate into unsafe situations. As safety professionals, we often find ourselves offering support for off-the-job safety and, in this case, understanding the realities of public demonstrations, protests, and the legal and physical boundaries that accompany them.
With news cycles spinning at full speed and emotions often running high, many workers have legitimate questions about their rights and responsibilities. Can they protest? Where? What happens if the situation turns volatile? More importantly, how can safety professionals engage in clear, respectful, and legally informed conversations with workers to help them protect themselves without discouraging their civil participation?
To do this, we must first provide the necessary context for understanding the First Amendment's protections, clarify common misconceptions, and give you practical talking points to help your teams navigate these complex situations.
What the First Amendment Protects—and What It Doesn't
The First Amendment of the U.S. Constitution protects the right of individuals to peaceably assemble, which means they can gather in public to express their views without fear of government retaliation, as long as the assembly is nonviolent. This right typically applies to traditional public forums such as sidewalks, parks, streets, and public plazas. However, the government can impose reasonable restrictions on the time, place, and manner of protests as long as those rules are content-neutral, serve a legitimate public interest (such as safety or order), and leave open alternative channels for expression. For example, cities may require protest permits to ensure public safety and traffic flow, and it is legal for them to do so.
This constitutional protection does not extend to violent gatherings, riots, or demonstrations that damage property or obstruct critical public functions. Protesters do not have the right to block streets, traffic, or access to government buildings unless local authorities permit such actions. Likewise, they cannot protest on private property without the owner's consent. Participation in unlawful activity—even within a larger peaceful protest—can result in arrest or other legal consequences.
Several key Supreme Court cases clarify these boundaries. In Cox v. Louisiana (1965), the Court upheld restrictions against protests that block public access to government functions. To quote from the decision:
"The constitutional guarantee of liberty implies the existence of an organized society maintaining public order, without which liberty itself would be lost in the excesses of anarchy. The control of travel on the streets is a clear example of governmental responsibility to insure this necessary order. One would not be justified in ignoring the familiar red light because this was thought to be a means of social protest. Nor could one, contrary to traffic regulations, insist upon a street meeting in the middle of Times Square at the rush hour as a form of freedom of speech or assembly. Governmental authorities have the duty and responsibility to keep their streets open and available for movement. A group of demonstrators could not insist upon the right to cordon off street, or entrance to a public or private building, and allow no one to pass who did not agree to listen to their exhortations."
In Clark v. Community for Creative Non-Violence(1984), the Court supported limits on protest locations when the rules were content-neutral and preserved the public's use of the space. In 1982, the National Park Service issued a permit to Community for Creative Non-Violence (CCNV) to conduct a demonstration in Lafayette Park and the Mall, which are National Parks in the heart of Washington, D.C. However, the Park Service, relying on its regulations, particularly one that permits "camping" (defined as including sleeping activities) only in designated campgrounds, no campgrounds having ever been designated in Lafayette Park or the Mall, denied CCNV's request that demonstrators be permitted to sleep in the symbolic tents.
The regulation forbidding sleeping meets the requirements for a reasonable time, place, or manner restriction of expression, whether oral, written, or symbolized by conduct. The regulation is neutral regarding the message presented and leaves open ample alternative methods of communicating the intended message.
Ward v. Rock Against Racism (1989) further affirmed that time, place, and manner restrictions are valid if they are narrowly tailored and do not target the content of the protest. Rock Against Racism was a performance group seeking to use the bandshell pavilion for a concert. New York City imposed regulations on the use of the bandshell in Central Park, seeking to control the sound volume of concerts there. The City provided sound amplification equipment and a sound technician for the performers to use, and they were required to use them. There was no substantial burden here since the concerts could continue with adequate equipment, and the restriction was content-neutral. It was justifiable for the City to prevent the sound from interfering with people in quieter surrounding areas.
Meanwhile, Adderley v. Florida (1966) clarified that the government can prohibit protests on certain public properties—like jails or military installations—that are not traditionally open to the public. A group of students was protesting on a nonpublic jail driveway, which they blocked to demonstrate against their schoolmates' arrest. The sheriff advised them that they were trespassing on county property and would have to leave or be arrested. The demonstrators refusing to leave were then arrested and convicted under a Florida trespass statute. The protestors claimed that their convictions deprived them of their "rights of free speech, assembly, petition, due process of law, and equal protection under the laws" under the Fourteenth Amendment. The Judges found that there was ample evidence to support the protestors' trespass convictions for remaining on jail grounds reserved for jail uses after they had been directed to leave by the sheriff. There was no evidence that protestors were arrested or convicted for their views or objectives. Furthermore, they affirmed:
"The rights of free speech and assembly, while fundamental in our democratic society, still do not mean that everyone with opinions or beliefs to express may address a group at any public place and at any time. The constitutional guarantee of liberty implies the existence of an organized society maintaining public order, without which liberty itself would be lost in the excesses of anarchy. . . . A group of demonstrators could not insist upon the right to cordon off a street, or entrance to a public or private building, and allow no one to pass who did not agree to listen to their exhortations."
Putting it into Practice
For safety professionals, it's critical to understand and communicate this balance. Workers should be encouraged to express themselves lawfully and peacefully. Still, they must also understand the limits of their rights and the potential legal and safety risks associated with their actions. Participating in protests on public sidewalks or in designated areas is typically lawful, provided they do not block traffic or access to buildings. Remember, the general public has a right to freedom of movement that the police will protect.
Disorderly conduct is the most frequently cited violation that can land a protester in legal trouble. Here are just a few examples of unprotected disorderly conduct that might arise at a protest:
- Blocking/preventing access to abuilding
- Disrupting normal official business/operations
- Harassing someone by blocking their free movement in a public way, such as roads and sidewalks
- Forcing the public to listen to an unwanted message (not letting people pass)
- Fighting words
- Making noise in a residential neighborhood in violation of local ordinacnes
- Disrupting a government hearing by standing and shouting in the hearing room
It's also important to respect local laws and ordinances, including any curfews or permit requirements that may apply. Workers should be reminded that their actions during protests can have personal and professional consequences, especially if they engage in illegal conduct or violate employer policies, such as participating while wearing company uniforms or during paid work hours.
A practical way to convey this message might be:
"We fully support everyone's constitutional rights, including the right to peaceably assemble. If you choose to protest, please do so safely and lawfully. Stay in public areas that are open to assembly, avoid blocking streets or entrances to public buildings, and follow lawful police instructions. Your voice matters—and so does your safety."
Helping workers understand these nuances allows safety professionals to maintain a respectful, informed, and safety-focused dialogue during turbulent times, protecting both individual rights and worker safety. Remember:
- Blocking Entrances and Traffic: Protesters can be arrested for blocking building entrances or obstructing pedestrian and vehicle traffic, as these actions directly interfere with the public's right to use public spaces. Interference with government functions can be a federal offense, which includes obstruction with the intent to disrupt or impede government business.
- Permit Requirements: For larger demonstrations that may require street closures or special accommodations, obtaining a permit is a common requirement to help manage traffic and logistics without preventing the protest itself.
- Noise Regulations: The government can regulate the use of sound amplification devices to prevent excessive noise that would disrupt normal operations.
Conclusion: Leading with Clarity and Compassion
Protests are not new, but the way we engage with them as professionals must evolve. Whether due to social media influence, lack of civics education, or local officials tolerating illegal behavior, many protests today can easily violate the law. The First Amendment is often invoked to justify forcing others to listen to a message, restricting their freedom of movement, or even destroying property - this is not protected speech. More often than not, the speech (the overall message) is not the issue; rather, it is an issue with the right to peaceable assembly, a part of the First Amendment that is often overlooked or misinterpreted.
Whether your team members are directly participating in demonstrations or may encounter them during work-related travel or commuting, you need to provide clear guidance that respects both their rights and their safety. As a safety leader, your credibility rests not just on knowing the law but on being able to translate that knowledge into calm, practical advice during moments of uncertainty.
Encourage lawful, peaceful participation where appropriate. Make sure your workers understand where those boundaries lie—and where the risks begin. Most of all, create an environment where they feel comfortable coming to you with questions, knowing that your goal is not to control or stifle but to support and protect.
Helping people stay safe sometimes means knowing when to step back and when to speak up. Let’s make sure they’re equipped to do both.
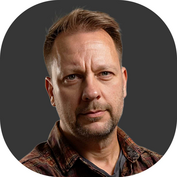
Blaine J. Hoffmann, MS OSHM, has been in the occupational safety & health industry for over 28 years and is the author of Rethinking SAFETY Culture and Rethinking SAFETY Communications. Blaine is the producer and host of The SafetyPro Podcast and founded the SafetyPro Podcast community site.