Workplace incidents are never something that employers and employees look forward to experiencing. However, they do happen, and it's important for everyone involved to understand what happened and how it happened, which will require you to interview those involved in the incident. So, it stands to reason you will want to ask the right questions correctly to elicit the most accurate information possible. A cognitive interview technique is one of the most effective ways to do this.
What is a Cognitive Interview Technique?
A cognitive interview technique is a method of questioning designed to encourage interviewees to provide as much detail as possible about an incident. It's called "cognitive" because it focuses on people's mental processes for remembering events. It is based on the idea that memory is constructive; our memories are not perfect representations of what happened but reconstructions of what we think we experienced.
There are several benefits to using a cognitive interview technique for workplace incidents:
- Obtain Detailed and Accurate Information
Cognitive interviews are designed to gather as much detailed and accurate information about the incident as possible. This information can help you understand what happened, how it happened, and how to prevent it from happening again. Cognitive interviews can help establish a consistent timeline and identify discrepancies in the accounts in cases with multiple witnesses to an incident. - Prevention
Investigating workplace incidents is essential for preventing future incidents. By using cognitive interviews to gather information about an incident, you can identify its underlying causes and take corrective action to prevent similar incidents from happening in the future. - Continuous improvement
Workplace incidents can provide valuable insights into other areas where improvements can be made. By using cognitive interviews to gather information about an incident, you can identify opportunities for improvement and implement changes to prevent related incidents from occurring in other processes or areas of the workplace. - Employee engagement
Using cognitive interviews as part of the incident investigation process can also help engage employees. By encouraging employees to share their experiences and perspectives on the incident, you can demonstrate commitment to workplace safety, build trust with employees, and create a more robust safety culture. - Compliance
In many industries, employers are required by law to investigate workplace incidents. Using cognitive interviews as part of the incident investigation process can help one meet legal requirements and comply with regulations. Thoroughly investigating workplace safety incidents and taking corrective action can demonstrate that the company is taking the necessary steps to ensure the safety of its employees, which can help reduce the likelihood of legal action being taken.
How to Conduct a Cognitive Interview
During a cognitive interview, the interviewer may use several techniques that encourage the interviewee to provide a detailed description of the incident. When conducting a cognitive interview, following a structured approach is essential. Here are some techniques for conducting a successful cognitive interview:
- Establish rapport with the interviewee: Before the interview begins, the interviewee should feel comfortable and at ease. Establishing rapport can help put the interviewee at ease and encourage them to provide more detailed information.
- Ask Open-Ended Questions: Open-ended questions encourage the interviewee to provide a detailed description of the incident. They should be asked in a non-leading way to avoid influencing the interviewee's memory.
- Free recall: In this technique, the interviewer asks the interviewee to provide a complete account of the event without interruption. This technique encourages the interviewee to recall as much detail as possible without being influenced by the interviewer.
- Mental reinstatement: This technique involves asking the interviewee to mentally recreate the context and environment of the event. The interviewee is encouraged to recall sensory details such as sounds, smells, and colors to aid in recalling the event.
- Change perspective: In this technique, the interviewee is asked to recall the event from different perspectives, such as from the viewpoint of another person present during the event. This technique can help to uncover new details and views on the event.
- Repeated retrieval: This technique involves asking the interviewee to recall the event multiple times. It can help consolidate memories and recall information that may have been missed in previous interviews.
- Timeline: This technique involves asking the interviewee to provide a chronological event timeline. This technique can help identify discrepancies or inconsistencies in the interviewee's event account.
These techniques are used in different combinations depending on the specific needs of the investigation. By properly using these techniques, investigators can elicit more accurate and detailed information about an event, which can be used to prevent future incidents and ensure workplace safety.
Pro Tip: Building Backward
One powerful twist to applying the timeline technique mentioned above is asking an interviewee to remember workplace incident events in reverse order. There are several benefits when asking someone to place events in an order they may not be used to recalling:
- Encourages a Different Recall Method: Asking an interviewee to recall the events of an incident in reverse order can help stimulate a different recall method. Typically, people tend to remember events in the order they happened. However, asking them to recall events in reverse order can encourage them to think more deeply about the incident. It may highlight details they may have forgotten or missed when remembering events chronologically.
- It helps to Identify Inaccuracies or Discrepancies in the Interviewee's Account: Recalling events in reverse order can help interviewers identify inaccuracies or discrepancies in the interviewee's account of the incident. If an interviewee's account changes or becomes unclear when recalling the events in reverse order, it may indicate that they are not being truthful or that their recollection of events is inaccurate.
- Reduces the Impact of Preconceptions and Expectations: Recalling events in reverse order can help reduce the impact of interviewees' preconceptions or expectations about the incident. Interviewees may have biases or assumptions about the sequence of events, and asking them to recall events in reverse order can help mitigate these biases and ensure that the account is more accurate.
Overall, asking an interviewee to recall workplace incident events in reverse order can help investigators gain a more accurate and detailed understanding of what happened.
It is essential to remember that conducting a cognitive interview for workplace incidents requires proper training and preparation. Interviewers must understand the mental processes involved in memory and the various techniques used in cognitive interviewing to ensure the interview is adequate and accurate.
Tips for Interview Success
First and foremost, it's essential to approach the worker with empathy and understanding. Recognize that they may be feeling anxious, upset, or even traumatized by the incident, and make it clear that you're there to support them and help them get through this difficult time.
Here are a few other tips that can help make the worker more comfortable:
- Start by thanking the worker for their time and willingness to talk to you. Let them know that you appreciate their help in understanding what happened and how to prevent it in the future.
- Create a safe and confidential space for the interview. Choose a private location where the worker won't be interrupted or overheard. Let them know that anything they say will be kept confidential and won't be used against them in any way. Don't place an object, like a desk, between you and the interviewee - sit with them. Let them sit near the door and give them a comfortable chair - all of these things can make the space safer for them to relax and feel more at ease.
- Be respectful and non-judgmental in your tone and body language. Don't interrupt the workers or argue with them, even if you disagree with what they're saying. Show that you're listening carefully and taking their words seriously.
- Offer support and resources if the worker needs them. Depending on the nature of the incident, they may need medical attention, counseling, or other types of assistance. Let them know that you're there to help and that you can connect them with any resources they need.
These are not interrogations, where you have evidence that they have done something wrong and need them to confess. They can help you learn how work happens so you can look for opportunities to improve together, so the event does not happen again. - Blaine J. Hoffmann, MS OSHM
Remember, the goal of the post-incident interview is to learn from what happened and prevent it from happening again. By approaching the worker with empathy and understanding, you can help them feel more comfortable and willing to share their experiences and insights.
Conclusion
In summary, cognitive interviews are an effective tool for investigating workplace incidents. By using cognitive interviews as part of your incident investigation process, you can improve the accuracy of your investigations, prevent future incidents, comply with legal requirements, engage employees, and continuously improve your workplace safety programs.
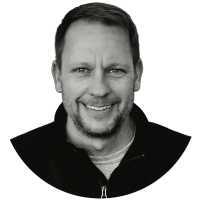
Blaine J. Hoffmann, MS OSHM has been in the occupational safety and health industry for over 28 years and is the author of "Rethinking SAFETY Culture" and "Rethinking SAFETY Communications," which are available now. Blaine is also the producer and host of The SafetyPro Podcast and founded the SafetyPro Podcast community site.