On February 3rd, 2023, a train carrying hazardous materials derailed near East Palestine, Ohio. The train carried various chemicals, including vinyl chloride, ethylhexyl acrylate, and ethylene glycol monobutyl. The derailment resulted in a fire, and chemical release into the surrounding environment, leading to the evacuation of residents.
The National Transportation Safety Board (NTSB) has launched an investigation into the incident to determine the cause and make recommendations to prevent similar accidents in the future.
One thing I noticed about the news coverage is the language; some call the chemicals hazardous, and some use the word toxic. So, which is it?
Were Hazardous Chemicals or Toxic Chemicals Involved? What's the Difference?
The U.S. government defines hazardous materials under the Hazardous Materials Transportation Act (HMTA) and its corresponding regulations, which the Pipeline and Hazardous Materials Safety Administration (PHMSA), an agency within the U.S. Department of Transportation, oversees.
These regulations broadly define hazardous materials as any substances or materials that pose an unreasonable risk to health, safety, or property when transported in commerce, including toxic, flammable, corrosive, explosive, radioactive, or otherwise dangerous substances.
To be more specific, the regulations list specific classes of hazardous materials based on their physical and chemical properties and potential hazards. These classes include explosives, gases, flammable liquids and solids, oxidizing substances, toxic substances, radioactive materials, corrosive substances, and miscellaneous dangerous goods.
If a substance falls under one of these classifications, it is considered a hazardous material and is subject to strict regulations for safe transportation in commerce. These regulations cover the packaging, labeling, marking, and handling hazardous materials to ensure they are transported safely and without incident.
So what are toxic chemicals? A material is toxic if it is capable of causing harm to human health, such as illness or injury, through ingestion, inhalation, or skin contact. Toxicity can be acute or chronic, and the degree of harm can depend on several factors, including the material's concentration, the exposure length, and the susceptibility of the exposed individual.
The Environmental Protection Agency (EPA) has also established a list of hazardous air pollutants (HAPs), including chemicals known or suspected to cause cancer, birth defects, or other serious health effects. HAPs are regulated under the Clean Air Act, and their emissions are subject to strict controls to protect human health and the environment.
As you can see, toxic is a category of hazardous materials. So, when you use the term "Hazardous Chemical," you may be referring to any of the categories listed under regulations, making it a generic label. But when you say "Toxic Chemicals," you refer to a specific hazardous chemical type.
All toxic chemicals are hazardous, but not all hazardous chemicals are toxic. You get the point - Blaine J. Hoffmann, MS OSHM
Chemicals Involved
There were reportedly several chemicals of concern involved in the train derailment.
Vinyl chloride is a colorless gas that produces polyvinyl chloride (PVC), a widely used plastic material. It is also an intermediate in making other chemicals, such as chlorinated solvents and pharmaceuticals.
Exposure to vinyl chloride can harm human health, and it is considered a toxic and carcinogenic substance, meaning it can cause cancer. Inhalation of vinyl chloride can irritate the respiratory system and cause dizziness, headaches, and fatigue. Long-term exposure to high levels of vinyl chloride has been linked to an increased risk of certain types of cancer, including liver cancer and angiosarcoma (rare cancer affecting the blood vessels).
Due to the health risks associated with vinyl chloride, it is strictly regulated by government agencies such as the Occupational Safety and Health Administration (OSHA) and the Environmental Protection Agency (EPA). These agencies have established exposure limits and other requirements to protect workers and the public from the harmful effects of vinyl chloride.
Ethylhexyl acrylate is a chemical compound belonging to the acrylic esters group. It is a clear, colorless liquid with a slightly pungent odor. It is used as a monomer in producing various polymers, including acrylic and copolymers.
Ethylhexyl acrylate is primarily used as a building block in synthesizing polymer-based products, such as adhesives, coatings, and elastomers. It is also a surfactant and an intermediate in producing other chemicals.
Exposure to ethylhexyl acrylate can irritate the eyes, skin, and respiratory tract, causing headaches and dizziness. It may also cause allergic reactions in some individuals. The International Agency for Research on Cancer (IARC) has classified ethylhexyl acrylate as a Group 2B carcinogen, which means it is possibly carcinogenic to humans based on animal studies. However, more research is needed to understand this substance's potential health effects fully.
Government agencies, such as the Occupational Safety and Health Administration (OSHA) and the Environmental Protection Agency (EPA), regulate ethylhexyl acrylate to protect workers and the public from potential health risks. These agencies have established exposure limits and other requirements for safely handling and using this substance.
Ethylene glycol monobutyl, or 2-butoxyethanol, is a clear, colorless liquid with a mild, sweet odor. It is a glycol ether used primarily as a solvent in various industrial and commercial applications.
Ethylene glycol monobutyl is used as a solvent in producing resins, lacquers, and other coatings. It is also used as a cleaning agent and in making various types of chemicals, including plasticizers, textile dyes, and pharmaceuticals.
Exposure to ethylene glycol monobutyl can irritate the eyes, skin, and respiratory tract and cause headaches, nausea, and dizziness. Long-term exposure to high levels of this substance can cause damage to the liver, kidneys, and blood cells. In addition, ethylene glycol monobutyl has been associated with developmental and reproductive effects in laboratory animals.
Government agencies, such as the Occupational Safety and Health Administration (OSHA) and the Environmental Protection Agency (EPA), regulate ethylene glycol monobutyl to protect workers and the public from potential health risks. These agencies have established exposure limits and other requirements for safely handling and using this substance.
Exposure limits to chemicals set by the government do not necessarily mean that there will be no harm, as the toxicity of chemicals can depend on various factors, including the level of exposure, the duration of exposure, and the individual's susceptibility to the effects of the chemical. These limits are designed to minimize the risk of adverse health effects to workers, consumers, and the general public - not eliminate the risks.
It is important to note that exposure to levels below the set limits may still cause adverse health effects, particularly for individuals more susceptible to the effects of the chemical, such as children, pregnant women, and people with pre-existing medical conditions.
Therefore, it is crucial to follow safety guidelines and precautions when working with or around hazardous chemicals, including using appropriate protective equipment, ensuring proper ventilation, and following safe handling and disposal procedures. It is also critical to seek medical attention if you observe any symptoms of exposure to chemicals.
What about risks due to mixing or by-products?
These chemicals could form hazardous by-products if accidentally mixed, combined, or burned.
For example, mixing vinyl chloride with ethylhexyl acrylate could form a polymer, which can release toxic fumes and cause respiratory irritation. Mixing vinyl chloride with ethylene glycol monobutyl could lead to the formation of other harmful compounds, including aldehydes and ketones, which can irritate the eyes, nose, and throat, as well as cause headaches and dizziness.
The exact by-products of combining these chemicals would depend on the specific conditions of the reaction, such as the amount of each chemical present, the temperature, and the presence of other reactive compounds. Handling, separately handling, and transporting these chemicals is essential to avoid accidental mixing and potential harm to human health and the environment. For example, if transporting these chemicals on the same train, you would want other train cars with inert materials, or even empty ones if possible, separating them in the event of an accident, like a derailment.
In addition to Vinyl chloride, ethylhexyl acrylate, and ethylene glycol monobutyl being hazardous chemicals in and of themselves, burning them can produce a variety of potentially hazardous by-products, including:
- Carbon monoxide and carbon dioxide: These are typical by-products of the combustion of most hydrocarbons and can contribute to local air quality issues.
- Hydrogen chloride: This corrosive gas can cause respiratory and skin irritation and contribute to acid rain.
- Dioxins and furans are highly toxic compounds produced when organic matter, such as plastics, is burned. They can cause various health effects, including cancer, reproductive and developmental problems, and immune system damage.
- Acrolein is a highly reactive and irritating gas that can cause respiratory and eye irritation and contribute to air pollution.
- Soot and particulate matter: These tiny particles can be released during combustion and contribute to air pollution and respiratory problems.
It is important to note that the by-products of burning these chemicals can vary depending on various factors, such as the temperature and duration of the burn, the presence of other substances, and the conditions of the combustion process. Therefore, taking appropriate precautions when handling, transporting, and disposing of these chemicals is essential to minimize the risk of harm to human health and the environment.
What about the environmental impact?
The Ohio Environmental Protection Agency received results from their water sampling of the five wells that feed into East Palestine's municipal water system. The results show no detection of contaminants associated with the derailment. The Ohio EPA said they are confident that the municipal water is safe to drink and have said steel casing protects the wells from contamination.
The Ohio EPA also recommends that residents with private wells schedule an appointment for well water testing by an independent consultant. The Ohio Department of Health encourages those with private wells to use bottled water until their well water testing results come back.
What about the Ohio River impact? Tiffani Kavalec, chief of the Division of Surface Water at the Ohio Environmental Protection Agency, said the chemicals spilled into the Ohio River. Still, since it is such an enormous body of water, it can dilute the chemicals quickly.
However, during a press conference, Ohio Department of Natural Resources director Mary Mertz said four tributaries over a space of 7.5 miles along the Ohio River are contaminated. Still, officials are confident those waterways are contained and do not affect municipal water supplies. Nevertheless, the contaminated waterways have led to the deaths of some 3,500 fish. According to Mertz, none of the 12 species of dead fish are threatened or endangered, and there was no impact on nonaquatic life.
The 111 water samples collected from the day of the derailment through February 14th, 2023, were tested for butyl acrylate, vinyl chloride, ethylene glycol monobutyl ether, and ethylhexyl acrylateno. The result showed no detectable levels of the chemicals.
The public perception of this being a more significant threat than authorities indicate stems from people seeing a plume or sheen on the water in the Ohio River. A visible plume on the water may indicate detectable levels of harmful chemicals, but it is not a reliable indicator.
Some chemicals can be harmful in small concentrations, while others may not pose a significant risk, even at high concentrations. The appearance of a plume can depend on various factors, such as the type of chemical, the quantity and duration of the release, and the characteristics of the water body.
To determine if there are detectable levels of harmful chemicals in the water, appropriate testing and analysis of water samples must occur, which can involve using specialized equipment to measure the concentration of specific chemicals or perform a broader screening of the water for a range of potential contaminants.
It is important to note that even if detectable levels of harmful chemicals are in the water, this does not necessarily mean that there is an immediate health risk. The risk to human health and the environment will depend on various factors, such as the toxicity and quantity of the chemical, the exposure pathway, and the population's sensitivity.
Conclusion
This article used a recent disaster to illustrate how the media, even as safety professionals, can create confusion and panic by using the wrong words to describe events and substances involved.
To be clear, this train derailment is a tragedy. Full stop. At the time of this publishing, the long-term impact of this tragedy is unclear. Regardless, the emotional impact is clear; residents have lost confidence in the local, state, and federal agencies and the rail carrier due to their response and various communications failures. What do you think? Be sure to leave your comments below.
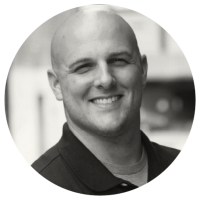
Drew Hinton is President/CEO of Arrow Safety and has 10 years of experience as a career Firefighter/EMT/HazMat Officer in Louisville (KY) and 15 years as a safety professional.
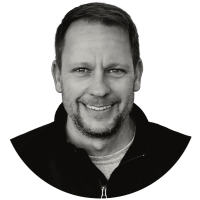
Blaine J. Hoffmann has been in the occupational safety & health industry for over 27 years. He is the producer and host of The SafetyPro Podcast and founded the SafetyPro Podcast Community Site.